“专精特新”光环加持,为何丢单?
最近笔者公司洽谈了一笔组合机床业务,项目前期,技术在理论层面得到了客户认可。机床设计、预设数据及参数、核心零部件供应商数据都符合预定要求。进入实施阶段,所有零部件图纸、大型铸件图纸下发供应商生产制造,表面看上去一切进展顺利。选定的供应商均属于高新技术和“专精特新”企业。在众多光环的加持下,笔者对产品质量信心满满。
然而,机床在最终组装时却出现了问题,外购零部件精度、尺寸偏差没能达到图纸要求,热处理、公差、材料工艺也不达标,装配不得不陷入停滞。经过反复修改和返工,机床虽然组装完成,性能却难以满足客户要求。
核心零部件主轴的精度、转速和稳定性与供应商书面提供的数据相差较大,供应商前期承诺的控制系统达到国际先进水平也不符合事实。除了螺栓以外,原本依靠进口后改用国内“专精特新”企业生产的核心零部件产品均不达标,最终导致整套组合机床无法交付。
据笔者观察,这并非个例。目前,国内“专精特新”企业多数以产业形式存在,例如机床领域,企业通过采购全球核心零部件组装成一台机床,再申请“专精特新”认证。但真正的“专精特新”产品是机床的系统和核心零部件。
“专精特新”并不一定要去创新、开发新产品,而是将现有产品做到更优,实现进口替代。虽然国内部分中小企业能够制造出外观接近的产品,但产品质量却大打折扣。进口产品能用十年甚至更久,国产的不到两年便暴露出各种问题。而多数企业解决问题的方式只是简单进行更换,并没有对问题根源进行深究,甚至对问题视而不见。如果以这种方式做“专精特新”,很难实现真正的突破。
在高端数控机床领域,只有进口的核心零部件才能满足主轴高精度的要求。机床周边配套零件,例如高性能刀具、夾头、液压筒夹等均需进口,而这些进口零部件都是简单的纯机械结构,即便如此,国内企业也做不到。
以展头刀为例,国内十多家企业宣称参数超过进口品牌,但产品使用不到两个月,精度开始下降。即便是在制造精度较高的中国台湾,其同类产品精度也仅达到进口产品的60%左右。再比如床身铸造,我们明确写明了材料配比和铸件要求,采购价格甚至高出市场价一倍,但供应商的产品质量仍不达标。
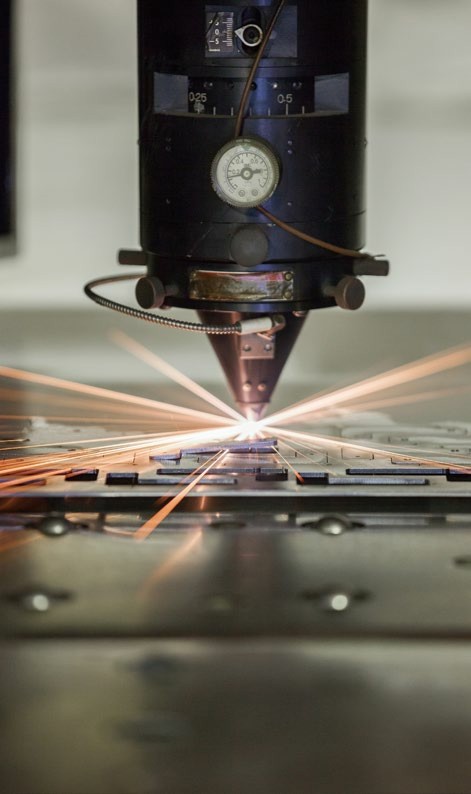
在制造业领域,企业无法掌握高附加值产品,根源在于没有在自身领域做到更好。当所有领域都不追求更好的时候,产业链也就处于低端水平。中国是产业链最完善的国家之一,但国内企业却造不出质量、性能与德国进口机床相媲美的产品。
笔者公司曾经想制造一根圆柱斜齿轴(德国进口零部件的一个核心零件),要求配合零间隙。整个机械加工圈子没有一家企业能够做到。或者材料性能不达标,或者涂层技术要求不达标,加上热处理磨削工艺更是很难做到。即便后期找到一家能做到的供应商,但由于报价高过进口1.5倍,自制还不如进口,于是我们只好放弃自制的想法。


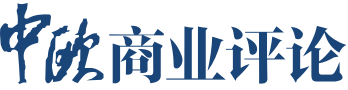
